反應(yīng)釜是聚酯裝置關(guān)鍵設(shè)備之一,終聚釜能否安全穩(wěn)定運行在很大程度上取決于液位變送器裝置的安全可靠性,終聚釜運行可靠性決定聚酯裝置能否長期、連續(xù)、穩(wěn)定、可靠運行。
我公司有一套 900 t /d 聚酯生產(chǎn)裝置,設(shè)計采用一套酯化線配二套縮聚生產(chǎn)線工藝。其中兩臺臥式帶有鼠籠式攪拌器的終聚釜,每臺鼠籠式攪拌器由兩根外置短軸支撐,每根短軸配置一套液位變送器。液位變送器為波紋管連接的背靠背、帶壓接觸式雙端面液位變送器。
1 反應(yīng)釜液位變送器裝置簡介
終聚釜雙端面液位變送器結(jié)構(gòu)見圖 1,具體工況如下:
水平安裝;
設(shè)計溫度: 300 ℃ ;
設(shè)計壓力: 真空/ + 0. 1 MPa;
密封介質(zhì): 聚酯熔體;
操作壓力: 0. 1 MPa;
操作溫度: 285 ~ 300 ℃ ;
沖洗方案: PLAN 54
阻封液: 乙二醇( EG) ;
沖洗液壓力: max. 0. 2 MPa;
轉(zhuǎn)速: 1. 5 ~ 6 r/min。
該液位變送器適用于較長的攪拌軸、高溫工況及溫度變化較大的臥式反應(yīng)釜。在密封殼體外配置金屬波紋管作為膨脹節(jié),金屬波紋管通過法蘭與釜體連接,金屬波紋管承受攪拌軸軸向延伸,避免由液位變送器件承受和補償攪拌軸產(chǎn)生的較大熱位移,同時金屬波紋管可以承受攪拌軸的徑向擺動。
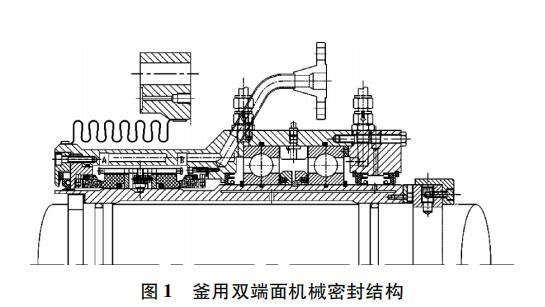
液位變送器運行的穩(wěn)定性、可靠性主要取決于密封端面油膜溫度。雙端面液位變送器工作時必須從外部引入與被密封介質(zhì)相容的密封流體,通常稱作阻封液( 或緩沖液) 。初始設(shè)置的釜用液位變送器輔助系統(tǒng)是為了給液位變送器提供清潔、冷卻、帶壓的阻封液,其主要功能是對密封端面的進行潤滑冷卻、平衡密封液的壓力,以改善密封端面間的運行條件,使液位變送器能夠長期、穩(wěn)定、可靠地運行。
2 初始配置的密封輔助系統(tǒng)存在缺陷
液位變送器初始配置 PLAN 54 沖洗冷卻方案。當(dāng)時為了考慮配置成本,沒有采用液位變送器制造商提供的密封輔助系統(tǒng),而是由生產(chǎn)裝置提供新鮮 EG用來沖洗、冷卻液位變送器,流程見圖 2。阻封液 EG與生產(chǎn)用 EG 共用同一臺輸送泵提供,泵出口主管道直徑為 DN150,阻封液主管徑為 DN40,阻封液主管裝配自力式調(diào)節(jié)閥,穩(wěn)定進入液位變送器系統(tǒng)的阻封液壓力,阻封液進入液位變送器管道管徑為 DN20。每臺釜用液位變送器進口安裝有手閥,出口裝配流量計、壓力表、溫度表和手閥,每臺液位變送器可以單好隔斷。
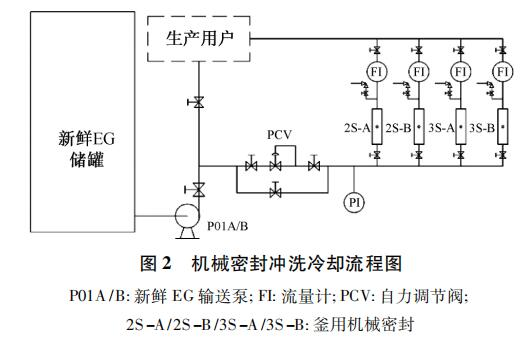
初始密封輔助系統(tǒng)存在以下缺陷:
1) 阻封液 EG 與生產(chǎn)用 EG 共用同一臺輸送泵,在生產(chǎn)過程中需要經(jīng)常配制添加劑,配制添加劑需用 EG 流量約為 20 m3 /h,生產(chǎn)穩(wěn)定、連續(xù)消耗 EG約為13 m3 /h,4 臺液位變送器( 2S -A/2S -B /3S -A/3S - B) 阻封液流量約為 2 m3 /h,在配制添加劑過程中,阻封液 EG 流量、壓力受影響很大,經(jīng)常導(dǎo)致阻封液EG 壓力、流量接近低報值。
2) 在生產(chǎn)裝置停機時,終聚釜操作溫度一般在約 290 ℃,終聚釜須依靠通氮氣降溫,通常要求溫度≤60 ℃才能停阻封液 EG,需要 2 ~ 3 天時間,這段時間消耗大量新鮮 EG,EG 只能當(dāng)作廢料處理,增加了生產(chǎn)車間的生產(chǎn)成本。
3) 受電網(wǎng)故障影響,一旦 EG 輸送泵斷電,釜用液位變送器處于無冷卻狀態(tài)。在原新鮮 EG 輸送泵配置 UPS 電源( 不間斷電源) 后,對外電網(wǎng)晃電有一定的改善,但當(dāng)外電網(wǎng)斷電時,仍會造成停供阻封液EG 的情況。
曾發(fā)生 1 起因外電網(wǎng)斷電導(dǎo)致液位變送器泄漏故障,發(fā)生 2 起因阻封液壓力流量低導(dǎo)致的液位變送器泄漏故障。
對于接觸式濕密封,維持密封腔壓力穩(wěn)定有利于保持足夠的汽化壓力裕量,可防止介質(zhì)流體在端面處局部汽化,有利于保護密封端面,反之,則會損壞密封端面。其中控制阻封液循環(huán)量是關(guān)鍵因素。密封腔熱量不及時帶走,液位變送器端面溫度過高會引起密封端面間油膜的氣化,使密封端面磨損,造成密封失效; 溫度升高也會使密封環(huán)變形,當(dāng)密封環(huán)所受熱應(yīng)力超過材料許用應(yīng)力時,密封件將發(fā)生永久變形破壞,造成密封端面接觸狀態(tài)的改變; 甚至因溫度變化引起熱沖擊和熱裂。 4) 運轉(zhuǎn)過程能耗較高。
3 改造方案
針對初始密封輔助系統(tǒng)的不足,提出改造成密封油站的方案,方案如下:
密封油站內(nèi)部增加配置潤滑油泵、冷卻器、油箱等設(shè)備。這種方案的優(yōu)勢在于 EG( 密封油) 可反復(fù)循環(huán)使用,直到不能滿足沖洗、冷卻要求后才更換新鮮 EG,隔離液循環(huán)動力強,循環(huán)流量較大,溫度進一步降低且可控,密封運行環(huán)境進一步改善。但密封油系統(tǒng)造價較高,對于單臺釜用液位變送器來說性價比不高,密封油站循環(huán)冷卻方案可同時配置多個釜用液位變送器。
3. 1 密封油站工作原理
密封油站主要包括密封油箱、蓄能器、油泵、換熱器、自力式調(diào)壓閥、過濾器及隨機儀表,并集成在同一底座內(nèi); 每臺密封沖洗支路上配置壓力表、壓力變送器、手動切斷閥、單向閥和轉(zhuǎn)子流量計,[1]詳見圖 3。
密封油經(jīng)油泵增壓后,送至各個高溫釜用液位變送器,系統(tǒng)的供油壓力通過自力式調(diào)節(jié)閥( PCV1) 調(diào) 節(jié),每個密封腔內(nèi)的密封油壓力通過支路手閥進行調(diào)節(jié)。
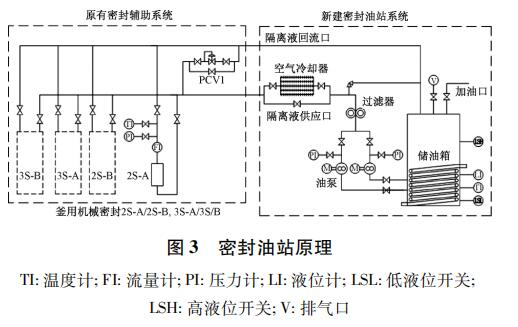
密封油站設(shè)計首先應(yīng)核算沖洗冷卻流量,根據(jù)沖洗流量來確定油箱容積,油箱容積一般為流量數(shù)值的 8 ~ 10 倍,空間允許盡量做大些。液壓元件選擇的通徑尺寸,應(yīng)不小于核算的管路通徑。為安全可靠,一般配置 2 臺油泵,可使用一臺備用一臺,檢修時可切換使用。配置 1 μm 精過濾器,避免雜質(zhì)進入密封腔。增設(shè)空氣冷卻器,氣溫低時可替代循環(huán)冷卻水。密封油選用清潔 EG。
3. 2 改造實施
在原有密封輔助系統(tǒng)的基礎(chǔ)上,增加配置密封油站,控制原理見圖 3。密封油站增加設(shè)備如下:儲液罐一臺( 利舊) ,容積 4 m3 /工作容積 3. 2 m3,裝配有低液位、高液位開關(guān),儲液罐安裝高度約3 m。
計量泵 2 臺,配置 G35 -1 單螺桿泵,流量 5 m3 / h,功率 2. 2 kW,配置變頻器,利于流量調(diào)節(jié)( 經(jīng)核算,4 臺液位變送器沖洗流量合計≥1. 98 m3 /h) ,為防止外 電 網(wǎng) 斷 電 停 泵,將電機并入現(xiàn)有 UPS 電 源系統(tǒng)。增設(shè)自制過濾器,材料選用 304 不銹鋼,裝配聚丙烯濾芯。
增設(shè)自制空氣冷卻器,材料選用 304 不銹鋼。
管路管徑選取 DN40,材質(zhì)選 用 304 不 銹 鋼, SH10S 壁厚系列,總長 150 m。
3. 3 密封泄漏判斷
當(dāng)巡檢人員觀察到油箱液位降低,或系統(tǒng)檢測到油箱低液位報警時,可確定多臺釜用液位變送器中有密封泄漏。操作人員可通過每臺液位變送器的回油流量與回油壓力判斷是否存在泄漏,通過泵轉(zhuǎn)速與回油總量可以估算泄漏量,決定是否需停機檢修。
3. 4 改造效果
2014 年對釜用液位變送器輔助系統(tǒng)改造后,密封油站已經(jīng)穩(wěn)定運行 4 年,阻封液回流壓力、流量穩(wěn)定,進口和出口的溫度差≤8 ℃。消除因裝置 EG 需求量波動和裝置停機對釜用液位變送器的影響,提高了釜用液位變送器運行的穩(wěn)定性、可靠性; 也解決了裝置停工過程中乙二醇耗量過大的問題; 同時還降低了裝置的公用工程消耗,與原輔助系統(tǒng)相比較,密封油站運行每年節(jié)約用電約 5 萬 kW·h。
4 結(jié) 論
密封油站循環(huán)冷卻方案可配置多個釜用機封,此方案已在石油化工行業(yè)的關(guān)鍵攪拌設(shè)備上廣泛應(yīng)用。Plan54 密封沖洗方案及密封油站的配套應(yīng)用,對聚酯裝置多臺釜用液位變送器和高溫油泵群液位變送器沖洗冷卻輔助系統(tǒng)是一個經(jīng)濟、可靠的選擇。